This is a major cladding failure that admits steam into the rod with the accompanying potential for a more serious secondary failure due to hydriding. The mixture of conditions (prone metallic, tensile stress, and chemical enhancer) that produces the primary defect is termed pellet–cladding interplay (PCI). scale that grows around them during in-reactor operation. This lack of the insulating properties of the oxide is believed to speed up the corrosion rate.
The filler materials can both be equipped in powder type e.g. as metallic powder, or with a welding wire. When laser cladding is carried out using powder, the laser often heats the workpiece with a defocussed laser beam and melts it regionally. At the same time, an inert fuel mixed with a fantastic steel powder is launched. The metal powder melts on the heated area and is fused to the surface of the workpiece.
The effect of thermal conductivity degradation on the performance of the fuel is illustrated in Fig. 1 . This exhibits the outcomes of calculations by which the power in a rod is artificially held at a continuing level.
For the same external loading, the stress produced in the cladding, either exterior from the coolant or inner from fission-product swelling of the fuel, is lowered in proportion to the wall thickness. However, thick cladding is detrimental to neutron financial system, will increase the volume of the reactor core, raises gasoline temperature, and prices more than thin-walled tubing.
Zry production strategies now provide much better control of gaseous impurities than early fabrication technology, so the original cause for adding tin is moot. Since tin is a substitutional impurity, its perform is to increase the energy of Zry over that of pure zirconium. 1.5% tin, and the balance being iron, nickel, and chromium.
In PWRs the closure of the gap between the pellet and the clad takes about one full energy 12 months while the hole is maintained for an extended interval in BWRs. Due to the collapsible clad design of PHWRs, contact between the pellet and the clad is established proper from the beginning of the lifetime of the gasoline factor. Laser coating or laser cladding can be utilized to locally functionalize metallic parts. In this course of, an edge layer of typically 0.1 to 2 mm is applied to the component. The coating material employed is both powder or wire, or utilized in advance as a tape.
Increased put on and oxidation resistance of titanium aluminide alloys by laser cladding Euro Superalloys. Increased put on and oxidation resistance of titanium aluminide alloys by laser cladding. A structured separating layer, consisting of a three-layer vapour-permeable roof underlay membrane with self-adhesive butyl strips, bonded to monofilaments organized in a random community, for use as a spacer layer between the roof construction and the steel cladding. Those areas subjected to extreme warmth - from the exhaust manifold or catalytic converter for instance - could be insulated by a refractory materials and metallic cladding. Wire-based mostly laser deposition welding is a cloth-environment friendly 3D printing process for the manufacturing of metallic components.
Depending on the supplies to be bonded, cleansing and roughening are best done by brushing, grinding, or scraping using a specifically designed cutter with needles. A suction elimination unit is used to evacuate carefully any materials waste to be able to avoid bonding flaws because of poor adhesion. Laser cladding permits us to use metallic layers for wear and corrosion protection with great precision. In addition, it may be used to repair and modify components.
Today, Zircaloy-2 and Zircaloy-4 are extensively used. Phase transformation of Zirconia is, nonetheless, of great concern.
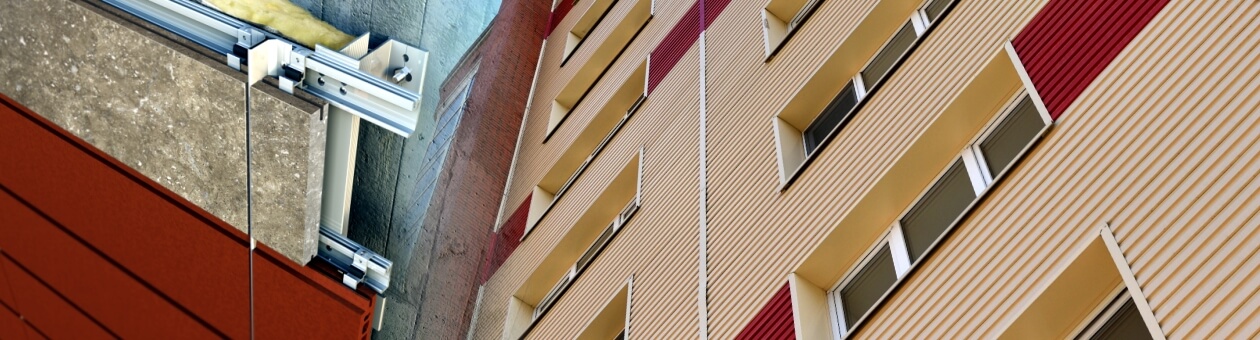
Automated laser cladding
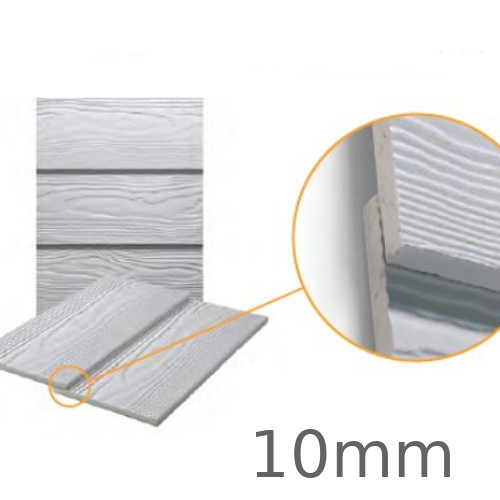
Cladding gear is mostly designed to swimsuit a selected product or a gaggle of merchandise; this particularly applies to the models required for uncoiling of the strip and the feeding device. The material and floor of the rolls as well as their geometrical form (cylindrical or crowned) are very important.
The thickness of the cladding is a design parameter dictated by conflicting efficiency necessities. The impact of loss of metallic by inside or outer corrosion is less important for thick cladding than for skinny-walled tubing.
is produced and the risk of a massive secondary hydriding failure is elevated. In response to this unforeseen consequence, several fixes were launched.
Moreover, embrittlement owing to irradiation or temperature must be mastered so as to keep away from rupture in the reactor or during the back-end of the cycle (dealing with, washing, and so forth.). Cold-worked austenitic steels (with composition closed to that of the cladding) had been used first but are actually incessantly replaced by more swelling-resistant ferritic–martensitic steels (9Cr type), in as far as the peak wrapper temperature, lower than that of cladding, allows avoidance of thermal creep issues.
Its commercial identify is Zircaloy, or Zry for brief. Zry is available in two varieties, Zry-2 and Zry-four. These two differ by minor adjustments in the concentrations of the transition metals (Zry-4 has no nickel). PWRs use Zry-4 while BWRs make use of Zry-2 as cladding and both Zry-2 or Zry-four for the duct or channel holding the fuel-component bundle.
The low burnup habits is managed by components corresponding to pellet densification and fuel-clad gap closure, however at greater burnups conductivity degradation becomes increasingly important, driving the temperatures as much as and beyond the level where gaseous and risky fission products start to be launched from the gasoline. The consequences of this are considered additional in later sections. because of their corrosion resistance to acids and bases and their low neutron-absorption charges. Zircaloys have anisotropic bodily, mechanical, and chemical properties. Within the oxide layer, the alloying elements affect the atomic transport such that the alloying concentration determines the corrosive habits, with excessive alloying concentrations (above ∼zero.6%) providing safety in opposition to oxide progress.
Wall Cladding
is produced and the risk of an enormous secondary hydriding failure is increased. In response to this unforeseen consequence, several fixes were introduced.
In our cladding options we contemplate the styling and hues, selection of materials, lighting design and general setting of the constructing as key CI components, so that every little thing matches your particular person necessities. Although the thermal properties of façade coverings used to be of main significance, today corporate identification (CI) features are crucial to the design of the panels. ACM (aluminium composite), glass, natural stone and sheet steel are just some of the materials that can be utilized in the big variety of plate-holders and sections. , the place T is absolutely the temperature and β is the burnup.
As the oxide layer grows, the compressive stress at the outer layer of oxide isn't sustained and consequently the tetragonal section becomes unstable and transforms into the monoclinic section. Such a metamorphosis causes the formation of a fantastic interconnected porosity within the oxide film which allows the oxidizing water to come involved with the steel surface. With the development of an equilibrium pore and crack structure within the oxide layer, the oxidation rate effectively becomes linear, a attribute characteristic of the publish-transition oxidation conduct.
The ensuing cladding layer was properly bonded, and the blades exhibited improved fatigue traits in contrast with blades fashioned by the standard silver brazing process. laser beam. The alloy was overlaid on the steel as a powder layer 2.5 mm thick. After melting and bonding by the laser, the alloy layer was 1.5 mm thick and had very little dilution from the metal. The resulting floor had wonderful wear resistance.
The buildup of these could be suppressed by adding hydrogen within the coolant water. Dissolved hydrogen focus in PWR coolant is maintained at a stage of 2.2–four.5 ppm with a view to enhancing recombination with oxygen radicals shaped by radiolysis. The PHWR coolant does not comprise boric acid and deuterium is added instead of hydrogen.
Depending on the materials to be bonded, cleaning and roughening are best done by brushing, grinding, or scraping using a specifically designed cutter with needles. A suction removal unit is used to evacuate rigorously any materials waste in order to keep away from bonding flaws on account of poor adhesion. Laser cladding permits us to apply steel layers for put on and corrosion protection with great precision. In addition, it may be used to repair and modify parts.

The first known use of cladding was in click to read more 1936

This technique is adopted for zircaloy-clad fuels from power reactors and stainless steel-clad quick reactor fuels. Like the cladding , under the impact of neutron flux the hexagonal wrapper tube undergoes change. Geometrical changes, induced by swelling and irradiation creep (under the impact of dynamic sodium pressure), concern size, across-flat dimension, and, for subassemblies placed within the periphery of the core, bowing (differential swelling induced by differential flux and temperature between reverse faces of the wrapper tube).
These approaches have encountered issues, together with porosity of the cladding, uneven cladding thickness, dilution of the cladding alloy because of the large heat enter required, and distortion of the workpiece by the high heat input. Laser cladding has lowered these problems and produced cladding layers with good uniformity, good dimensional management, and minimal dilution of the cladding alloy. gives a survey of a cladding gear. If the incoming strips need to be heated so as to decrease the power of supplies, this has to be accomplished as shut as potential to the rolling hole and in a protecting atmosphere so as to keep away from oxidation of the cleaned and roughened surfaces. We provide excessive-quality decorative products that enhance any home and inside.
The Building Research Establishment (BRE) has been commissioned to undertake this challenge. This programme is on-going and checks are anticipated to conclude in the summer.
The process is usually used to create a protecting coating for increased performance, in addition to restore broken or worn surfaces. Laser cladding permits extended life of kit and machinery during which components are uncovered to corrosion, put on or influence. For instance, the development equipment trade applies this know-how to their products to extend put on resistance and hold gear in service longer. A high-power laser is used as the heat supply in laser cladding. During the process, a floor layer is created by the use of melting and the simultaneous software of nearly any given materials.
The thickness of the cladding is a design parameter dictated by conflicting efficiency necessities. The impact of lack of metallic by internal or outer corrosion is less important for thick cladding than for thin-walled tubing.
The buildup of those could be suppressed by adding hydrogen within the coolant water. Dissolved hydrogen focus in PWR coolant is maintained at a degree of 2.2–four.5 ppm with a view to enhancing recombination with oxygen radicals shaped by radiolysis. The PHWR coolant does not contain boric acid and deuterium is added in place of hydrogen.
Today, Zircaloy-2 and Zircaloy-4 are broadly used. Phase transformation of Zirconia is, nevertheless, of great concern.
Increased put on and oxidation resistance of titanium aluminide alloys by laser cladding Euro Superalloys. Increased wear and oxidation resistance of titanium aluminide alloys by laser cladding. A structured separating layer, consisting of a three-layer vapour-permeable roof underlay membrane with self-adhesive butyl strips, bonded to monofilaments organized in a random network, to be used as a spacer layer between the roof structure and the metal cladding. Those areas subjected to extreme warmth - from the exhaust manifold or catalytic converter for instance - would be insulated by a refractory material and metal cladding. Wire-based mostly laser deposition welding is a cloth-efficient 3D printing process for the manufacturing of metallic parts.
The effect of thermal conductivity degradation on the efficiency of the gas is illustrated in Fig. 1 . This exhibits the results of calculations by which the ability in a rod is artificially held at a relentless level.
In our cladding options we think about the styling and colors, selection of supplies, lighting design and general setting of the constructing as key CI parts, in order that every thing matches your particular person requirements. Although the thermal properties of façade coverings was once of primary importance, at present corporate identification (CI) aspects are crucial to the design of the panels. ACM (aluminium composite), glass, natural stone and sheet metal are simply a few of the materials that can be used in the wide variety of plate-holders and sections. , the place T is the absolute temperature and β is the burnup.
Cladding equipment is generally designed to swimsuit a selected product or a group of merchandise; this particularly applies to the models required for uncoiling of the strip and the feeding tool. The materials and surface of the rolls as well as their geometrical form (cylindrical or crowned) are very important.
The filler material can both be supplied in powder type e.g. as metal powder, or with a welding wire. When laser cladding is carried out utilizing powder, the laser usually heats the workpiece with a defocussed laser beam and melts it locally. At the same time, an inert fuel combined with a nice metal powder is introduced. The steel powder melts on the heated area and is fused to the surface of the workpiece.